PROFINET
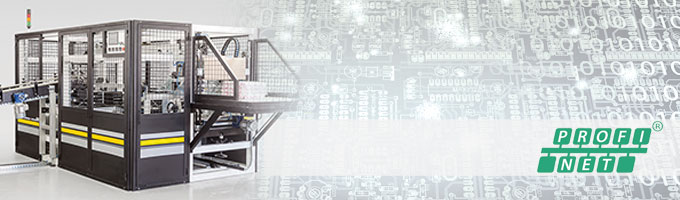
What is PROFINET?
The PROFINET protocol is based on Industrial Ethernet and is a communication standard for factory automation. It describes the entire data exchange between so-called slaves, such as Turck's multiprotocol I/O modules, and a controller (the PROFINET master). In this function, PROFINET is considered the successor to the PROFIBUS fieldbus protocol.
PROFINET was optimized in the area of cyclical data exchange and offers several new functions and extensions compared to conventional fieldbuses, particularly in relation to parameterization and diagnostics.
PROFINET offers users flexibility in the design of their network structures and enables them to transfer both process data in real-time (RT) as well as additional IT data via a single cable.
The system overview provides an initial impression of the network architecture and the different I/O and network components. Connections can be implemented via linear, star and tree structures, or also via a redundant ring topology (MRP).
Integration in process automation
Chemical and pharmaceutical plants must be protected at great expense from downtimes and therefore place particular requirements on I/O systems. The risk of explosion is present in many areas of a plant and an interruption in the continuous production process may result in enormous financial losses. To prevent this, controllers and I/O modules in the field are normally designed with redundancy, i.e.: if a device or a connection fails, the backup solution is activated.
Profinet System Redundancy
In the Profinet context, a new standard was created for this with system redundancy, offering greater investment security for companies in the process automation industry. The terminology used here is based on a classification that reflects the degree of fail safety that an automation system is to ensure.
No redundancy is implemented if a controller and field device only communicate via a single connection (S1). However, if a Profinet device supports communication relations to the primary controller as well as its backup via this one connection, this is classified as S2. This is the most commonly used form of system redundancy. The physical twin is activated if the main controller fails.
I/O devices from Turck can already maintain the required logical dual connection to two separate controllers. The TBEN-L5-8IOL is thus the world's first IO-Link master module with protection to IP67 to support Profinet S2 system redundancy.
Very high and maximum availability can only be achieved with R1 or R2 system redundancy. This involves the additional implementation on a field device of a redundant communication interface, and is used in conjunction with remote I/O. R2 with its four-way connection represents the highest level of complexity.
Smart combined with IO-Link
The Profinet extension for system redundancy now makes the benefits of Industrial Ethernet also available for the process industry. Turck goes one step further and additionally integrates IO-Link in the world of high availability systems. The overview shows what a system architecture could look like.
Nothing stands in the way of implementing the end-to-end digital linking of smart field devices, such as position indicators, valve blocks, sensors or I/O hubs. In terms of installation time, IO-Link is highly efficient and straightforward since data and power supply are transferred via a single unshielded standard cable.
Select Country
Turck worldwide