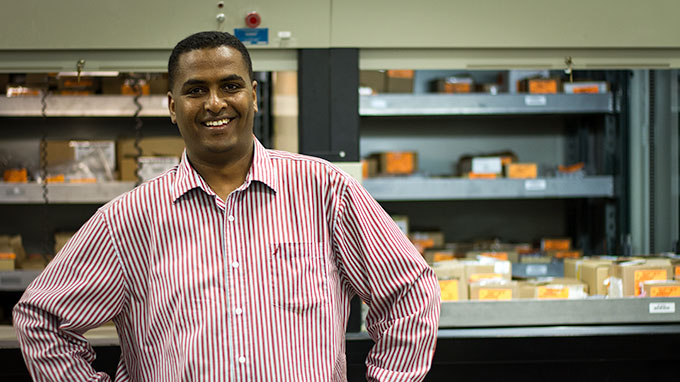
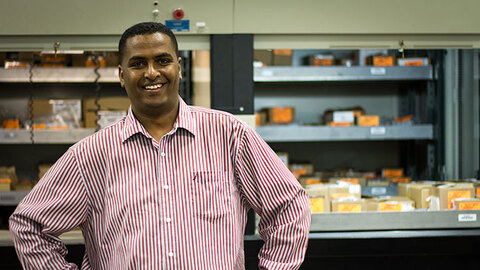
Frequently Asked Questions
Here you will find answers to the most commonly asked questions regarding products, technology, and applications.
Which cable tray best fits my application?
Please reference our Industrial Ethernet Cable Tray Guide for more information.
What does weld field immunity mean?
Many critical applications for proximity sensors involve their use in weld field environments. AC and DC resistance welders used in assembly equipment and other construction machines often require in excess of 20 kA to perform their weld function. Magnetic fields generated by these currents can cause false outputs in standard sensors.
Turck has pioneered the design and development of inductive proximity sensors that not only survive such environments, but also remain fully operative. Click here for more details.
How far do I have to mount my stainless steel sensors away from each other?
Please reference this handy chart to see mounting distances.
How does a DC sensor work in series / parallel?
Click here for the wiring diagrams for DC sensors.
What are the different DC outputs for sensors?
Two-, three-, and four-wire proximity sensors contain a transistor oscillator and a snap-action amplifier. This provides exceedingly high accuracy to a set switching point, even with very slowly approaching targets. Switching characteristics are unaffected by supply voltage fluctuations within the specified limits.
Click here to learn more about DC outputs.
How does an inductive sensor work?
An inductive proximity sensor consists of a coil and ferrite core arrangement, an oscillator and detector circuit, and a solid-state output. The oscillator creates a high frequency field radiating from the coil in front of the sensor, centered around the axis of the coil. The ferrite core bundles and directs the electro-magnetic field to the front.
When a metal object enters the high-frequency field, eddy currents are induced on the surface of the target. This results in a loss of energy in the oscillator circuit and, consequently, a smaller amplitude of oscillation. The detector circuit recognizes a specific change in amplitude and generates a signal which will turn the solid-state output “ON” or “OFF”. When the metal object leaves the sensing area, the oscillator regenerates, allowing the sensor to return to its normal state.
Click here to view a diagram of the operating principle for ferrite cores.
What affects my sensors operating distance?
Standard inductive sensors detect metals at different distances. To better understand correction factors and how they affect the sensing distance of your sensor, please click here.
What is a NAMUR output?
Click here to download Turck's technical reference regarding NAMUR sensor outputs.
How do I wire my NAMUR sensor?
To see how your NAMUR sensors would typically be installed into your intrinsically safe application, please click here.
How tight can I torque my locknut?
For Turck's maximum locknut torque specifications, please click here.
What types of materials does Turck use in construction?
For a full list of the materials that Turck uses, including the characteristics and why we use the materials we do, please click here.
How do you define a hazardous location?
To see a full explanation of how Classes, Divisions, and Groups are defined in hazardous locations, please click here.
Does Turck have a glossary of sensor terms I can reference?
We do. You can download by clicking here.
Does Turck have a glossary of Connectivity terms I can use?
We sure do! Download it right here.
What is a "Factor 1" sensor?
Factor 1 sensors (also known as Turck Uprox sensors) are sensors that have no reduction factor for different metallic compositions. This allows them to sense all metal targets at the same distance. Click here to see more characteristics of Turck's Uprox family of sensors.
What is the difference between embeddable and non-embeddable sensors?
Embeddable sensor construction includes a metal band that surrounds the ferrite core and coil arrangement. This helps to "bundle" or direct the electro-magnetic field to the front of the sensor.
Nonembeddable sensors do not have this metal band; therefore, they have a longer operating distance but are side sensitive.
Click here to download a diagram showing the difference.
How big of a hole do I drill for a metric thread?
Click here for a table converting hole size to thread size.
How do you convert AWG to metric?
Turck provides a handy conversion chart that includes a table converting AWG to metric, PG to metric, and a cable length tolerance chart. Click here to download it.
How should I mount my cable?
Proper management of cable systems can mean the difference between a dependable and smooth operating installation and costly reoccurring down time. Please click here to see a few helpful tips to consider when mounting your cable.
How do you wire AC sensors in series?
The maximum number of sensors to be operated in series depends on the stability of the line voltage and the operating characteristics of the load in question. Click here for more information on wiring AC sensors in series.
How do you wire AC sensors in parallel?
Click here to download the reference guide on parallel connections for AC proximity sensors.
How does an AC sensor work?
These sensors are used as pilot devices for AC-operated loads such as relays, contractors, solenoids, etc. AC sensors are typically available in a voltage range of 20-250 VAC. For more details, please click here.
How do I set up my IP address on a Turck Multiprotocol device?
Turck supports several methods to set or change the IP address across the product portfolio:
- IP Addressing via rotary switches or “Rotary Mode” - the last byte of the IP address is set with the rotary switches on the device
- “DHCP Mode” – IP values are assigned during device power-up
- “BOOTP Mode” – similar to DHCP
- Via PACTWare™ – device IP addresses can be changed via the device DTM through a frame application like PACTware™
- Via webserver – Turck devices contain an embedded webserver that will allow the user to assign an IP address via a supported web browser such as Microsoft Internet Explorer® or Google Chrome
What does Multiprotocol mean?
The Multiprotocol Ethernet concept is a technology pioneered by Turck to simplify Industrial Ethernet. Through an innovative approach to the operation of the station at the microprocessor level, Turck can deploy multiple Industrial Ethernet protocols in the same device.
The supported protocols include EtherNet/IP™, PROFINET® and Modbus™ TCP. The device will become a server on the network upon recognition of the network client upon power up. In other words, the master protocol will be served on a first-come, first-served basis.
For more information, visit our Multiprotocol Ethernet technology page.
What is sealed pressure?
Sealed pressure uses a pre-determined reference point, not necessarily vacuum. This allows for pressure measurement in locations that will vary with atmospheric changes.
What is gauge pressure?
Gauge pressure uses a reference to the atmosphere around the sensor. Because the sensing element has a deflection due to a pressure change, a reference point is needed to know exactly what pressure is being measured.
What is differential pressure?
Differential pressure can be a little more complex than gauge or absolute, but is simply measuring the difference between two medias.
What is absolute pressure?
Absolute pressure uses a reference to a perfect vacuum. This type of pressure reference is the gauge pressure of the media, in addition to the pressure of the atmosphere.
What is bonded pair?
Bonded pair cable is designed to not separate at the twist, thus preventing the separation of pairs. During installation, bonded pair cable reliably holds the twist of the pairs together to ensure they do not separate or fray at the ends. This allows for sufficient termination at the ends.
What is a twisted pair?
Twisted pair technology is made up of a series of two conductor pairs from the same circuit twisted together with the purpose of canceling electromagnetic interference (EMI).
What are the different types of pressure?
- PSI (Pounds per Square Inch): This is the unit of measure for one pound of force applied to one square inch of area. PSI is a typical unit of pressure in the United States.
- BAR: One bar is equal to the atmospheric pressure on the earth at sea level. BAR was a unit of measure created in Europe and is still commonly used there.
- PA (Pascal): This is the unit of measure for one newton of pressure per square meter.
- InHg (Inches of Mercury): This is the unit of measure for a one inch circular column of mercury, one inch tall, at gravity and 0 °C (32 °F). InHg is typically used as a unit of measure for barometric pressure.
- Torr: This unit was initially developed as a millimeter of mercury and is a very small fraction of atmospheric pressure.
- InH2O (Inches of Water): This is the unit of measure for a one inch circular column of water, one inch tall, at gravity and 4 °C (39.2 °F). InH2O is typically used for a differential pressure measurement or in low pressure water applications, such as level.
Ask your Question
Select Country
Turck worldwide